This information comes from James Taylor's facebook page:
The P5 models are unquestionably my favourite Rovers, and it was a 1963 3-litre Mk IIB automatic saloon that was my entry to Rover ownership in 1976. I still think that they were one of the great classics: among the most elegant, stylish and refined British cars of their era, they are still enormous fun today. I don’t have one on the fleet at the moment (more’s the pity). I sold my last one some time around 2011, and since then prices have crept up to a level where I’d have to think twice before trying to buy it back.
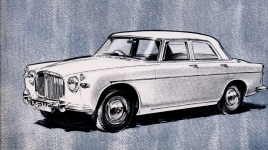
One of the aspects of these cars that hasn’t been very well covered is the assembly process. It both surprises and annoys me that I don’t have a definitive account of the way the P5 and P5B cars were built; in fact, my archive only contains pictures of early 3-litres on the assembly lines. If anybody has any assembly-line pictures of the later 3-litres or the V8-engined 3.5-litre cars, please feel free to add them in the Comments.
The account I’ve prepared below is a reconstruction based on what little evidence I have. It may therefore contain inaccuracies!
Building the Rover P5
Assembly of the Rover P5 3-litre and P5B 3.5-litre models at Solihull was always in the South Block. Now known as Block 1 (and in recent years completely rebuilt behind its original facia), this was the original office block of the wartime aero engine factory, and for many years after the war also contained the Directors’ offices.
However, this was not where the manufacturing process began. The Rover assembly lines were fed by a number of outside suppliers and by other Rover factories. Engines and manual gearboxes came from Rover’s Acocks Green factory; overdrives came from Laycock Engineering in Sheffield; automatic gearboxes came from Borg Warner at Letchworth; I believe front sub-frames came from John Thompson Pressings in Wolverhampton; and of course the bodies came from the Pressed Steel factory at Swindon. (Body manufacture was later transferred to Pressed Steel’s Linwood plant in Scotland and eventually to its main Cowley site. It may be that the transfer to Cowley coincided with the start of P5B production in autumn 1967, but this is not confirmed.)
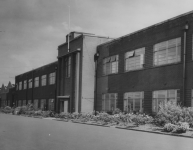
The bodies were delivered by road to the Rover factory, which had no direct rail link. They arrived as BIW (Body In White, ie bare metal) assemblies. As a first stage, their undersides were treated with Bittac sound-deadening compound (not underseal, as is sometimes suggested), and they were then primed and painted. From the Paint Shop, they passed to an initial preparation line that appears to have been the start of a U-shaped moving assembly line that ran up and down the length of the South Block. (As far as I know, there was only ever one assembly line for the P5 models, because they were built in relatively low volumes.) On this body preparation line, they received glass, window winding mechanisms, door lock mechanisms, and some lighting elements. Protective sheeting was then added before the next stage began.
The front-sub-frames were meanwhile put onto their own track in a separate sub-assembly area within the South Block, and here they were fitted with suspension and steering components, and with engines and transmissions. Each assembly was mounted on a trolley that ran on its own track, and was subsequently transferred to a main track where propshafts and rear axle assemblies were added. The rear axle, with its leaf springs attached, was mounted in a special rocking frame to aid positioning during assembly.
Each drivetrain assembly then proceeded to the Body Mounting area, where the sheeted bodies were hoisted from their assembly track across to the drivetrain line, to be lowered onto a drivetrain and bolted to it. This was achieved from pits underneath the moving assembly line. The track then took the newly combined assemblies to the Body Trim area, where they were fitted with carpets, seats, other items of interior trim, brightwork and bumpers. I presume the instrument panels were also added at this stage of assembly rather than during the first stage of body assembly.
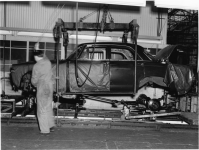
After the Body Trim stage came the Final Assembly stage, where wheels and tyres would be fitted, fluids and petrol would be added, and the cars would be started up for the first time. The next stage was a road test on the Test Track within the Solihull factory grounds, and after that they were driven to the Final Preparation area, where they would be polished and inspected under bright lights to show up any flaws. If the Inspectors were satisfied – and Rover had inspection stages all along the assembly line – the car would be handed over to the Despatch Department for onward transmission to the supplying dealer or to the docks (in the case of export models), or in some cases would be moved into a viewing area for direct delivery to customers who chose to collect their cars from the factory.
Assembly of the 3-litre P5 models ended in 1967 and the 3.5-litre P5B cars followed on the same assembly lines. Their production ended in June 1973, and the assembly area then stood idle until it was re-purposed during 1974 for assembly of the Land Rover 101 Forward Control military models.
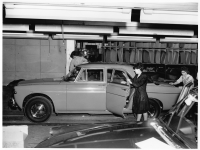
The P5 models are unquestionably my favourite Rovers, and it was a 1963 3-litre Mk IIB automatic saloon that was my entry to Rover ownership in 1976. I still think that they were one of the great classics: among the most elegant, stylish and refined British cars of their era, they are still enormous fun today. I don’t have one on the fleet at the moment (more’s the pity). I sold my last one some time around 2011, and since then prices have crept up to a level where I’d have to think twice before trying to buy it back.
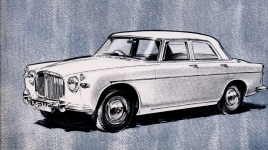
One of the aspects of these cars that hasn’t been very well covered is the assembly process. It both surprises and annoys me that I don’t have a definitive account of the way the P5 and P5B cars were built; in fact, my archive only contains pictures of early 3-litres on the assembly lines. If anybody has any assembly-line pictures of the later 3-litres or the V8-engined 3.5-litre cars, please feel free to add them in the Comments.
The account I’ve prepared below is a reconstruction based on what little evidence I have. It may therefore contain inaccuracies!
Building the Rover P5
Assembly of the Rover P5 3-litre and P5B 3.5-litre models at Solihull was always in the South Block. Now known as Block 1 (and in recent years completely rebuilt behind its original facia), this was the original office block of the wartime aero engine factory, and for many years after the war also contained the Directors’ offices.
However, this was not where the manufacturing process began. The Rover assembly lines were fed by a number of outside suppliers and by other Rover factories. Engines and manual gearboxes came from Rover’s Acocks Green factory; overdrives came from Laycock Engineering in Sheffield; automatic gearboxes came from Borg Warner at Letchworth; I believe front sub-frames came from John Thompson Pressings in Wolverhampton; and of course the bodies came from the Pressed Steel factory at Swindon. (Body manufacture was later transferred to Pressed Steel’s Linwood plant in Scotland and eventually to its main Cowley site. It may be that the transfer to Cowley coincided with the start of P5B production in autumn 1967, but this is not confirmed.)
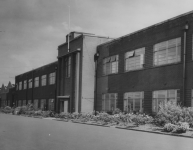
The bodies were delivered by road to the Rover factory, which had no direct rail link. They arrived as BIW (Body In White, ie bare metal) assemblies. As a first stage, their undersides were treated with Bittac sound-deadening compound (not underseal, as is sometimes suggested), and they were then primed and painted. From the Paint Shop, they passed to an initial preparation line that appears to have been the start of a U-shaped moving assembly line that ran up and down the length of the South Block. (As far as I know, there was only ever one assembly line for the P5 models, because they were built in relatively low volumes.) On this body preparation line, they received glass, window winding mechanisms, door lock mechanisms, and some lighting elements. Protective sheeting was then added before the next stage began.
The front-sub-frames were meanwhile put onto their own track in a separate sub-assembly area within the South Block, and here they were fitted with suspension and steering components, and with engines and transmissions. Each assembly was mounted on a trolley that ran on its own track, and was subsequently transferred to a main track where propshafts and rear axle assemblies were added. The rear axle, with its leaf springs attached, was mounted in a special rocking frame to aid positioning during assembly.
Each drivetrain assembly then proceeded to the Body Mounting area, where the sheeted bodies were hoisted from their assembly track across to the drivetrain line, to be lowered onto a drivetrain and bolted to it. This was achieved from pits underneath the moving assembly line. The track then took the newly combined assemblies to the Body Trim area, where they were fitted with carpets, seats, other items of interior trim, brightwork and bumpers. I presume the instrument panels were also added at this stage of assembly rather than during the first stage of body assembly.
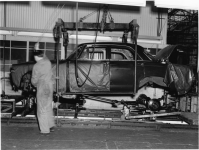
After the Body Trim stage came the Final Assembly stage, where wheels and tyres would be fitted, fluids and petrol would be added, and the cars would be started up for the first time. The next stage was a road test on the Test Track within the Solihull factory grounds, and after that they were driven to the Final Preparation area, where they would be polished and inspected under bright lights to show up any flaws. If the Inspectors were satisfied – and Rover had inspection stages all along the assembly line – the car would be handed over to the Despatch Department for onward transmission to the supplying dealer or to the docks (in the case of export models), or in some cases would be moved into a viewing area for direct delivery to customers who chose to collect their cars from the factory.
Assembly of the 3-litre P5 models ended in 1967 and the 3.5-litre P5B cars followed on the same assembly lines. Their production ended in June 1973, and the assembly area then stood idle until it was re-purposed during 1974 for assembly of the Land Rover 101 Forward Control military models.
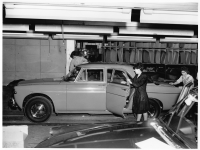